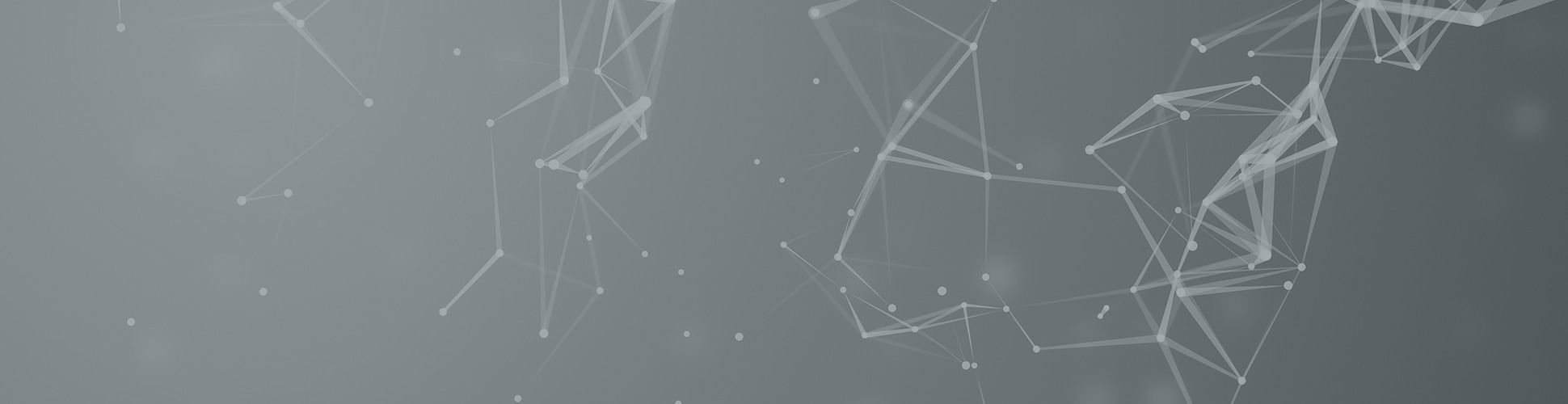
Get Prepared for New Plastic Packaging and Manufacturing Materials Requirements
Our experts break down how organizations can start planning today for new USP guidelines coming down the pike.
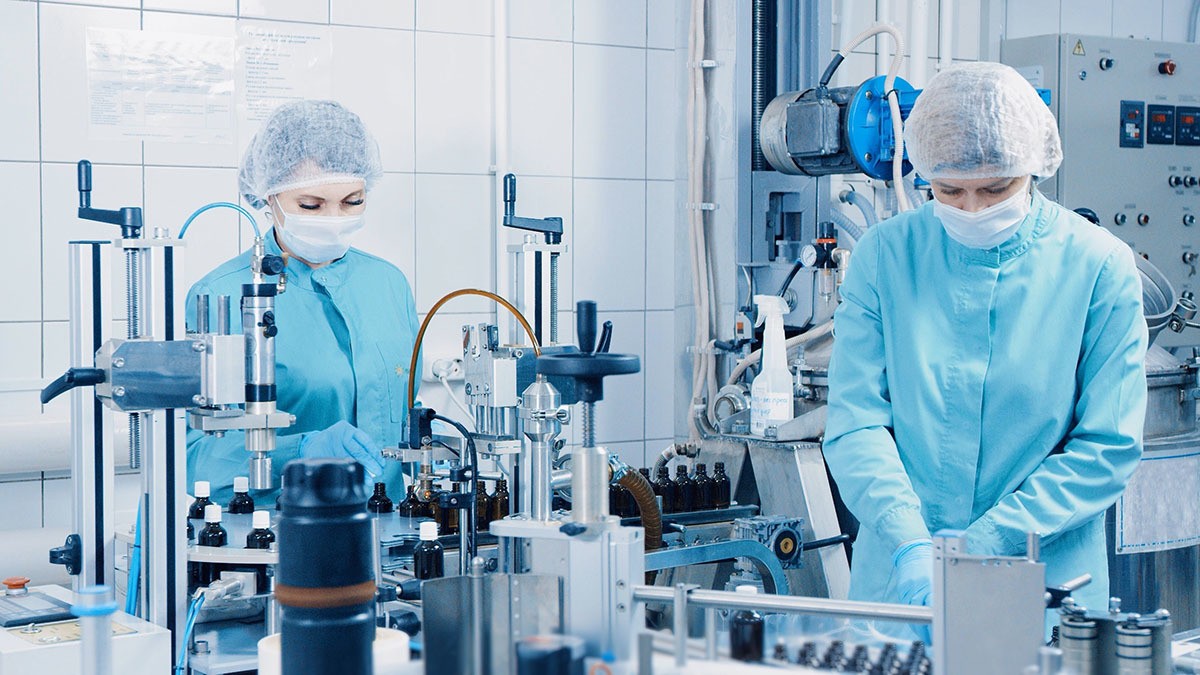
In clinical research, the role of drug packaging systems cannot be overlooked. Industry guidelines require biopharmaceutical and biotechnology companies to test their pharmaceutical packaging systems, as the systems often experience prolonged and intimate contact with drug products, drug substances and intermediates. Confirmation that no negative interactions take place is crucial to patient safety.
The United States Pharmacopeia (USP), an independent, scientific nonprofit whose standards ensure safety and quality in pharmaceutical development and manufacturing, has guidelines that cover packaging and container materials, including plastics (USP<661>), elastomeric components (USP<381>) and glass (USP<660>).
The USP-NF, the combined compendia of the USP and the National Formulary, is a method database for excipients and drug products and provides valuable information in general chapters. The USP also has guidelines and testing procedures prescribed in several chapters for glass and plastic containers and elastomeric closures. Characterizing materials prior to use is essential to ensuring safety of the materials as part of Quality by Design.
By Dec. 1, 2025, all plastic packaging and manufacturing materials for pharmaceutical use must meet the updated USP <661.2> and USP <661.1> requirements.
These updates are part of the continual effort by the USP and the U.S. Food and Drug Administration to ensure packaging safety.
Depending on the type of material and packaging, materials that previously complied with USP <661> may not meet the new requirements and will require retesting to comply with the USP.
For companies that do not have a dedicated, experienced laboratory partner, retesting packaging is a heavy lift with downstream impacts on patient safety. However, organizations that act now will avoid downstream interruptions when the new USP chapters in the current guidance take effect.
Key competencies for biotech and biopharma organizations to meet the new USP requirements for plastic packaging and manufacturing materials
With the implementation date drawing nearer, drug developers should test their packaging systems to ensure they are compliant and adhere to patient safety goals, or quickly identify and qualify alternatives. Our GMP Lab team, which provides PPD™ Laboratory services, has already received requests from clients who have chosen to transition as quickly as possible to stay ahead of these compliance requirements and perhaps be one step ahead of the competition.
- Compendial testing procedures: Compendial testing procedures that are verified or validated for each material in compliance with USP <1226> and USP <1225> ensure accurate and consistent testing. Drug developers should look to a partner, like the laboratory services team within the PPD™ clinical research business of Thermo Fisher Scientific, that is equipped with autoclaves and ovens capable of meeting the stringent compendial extraction requirements. In addition, our GMP Lab in Middleton, Wisconsin, houses a dedicated compendial testing laboratory with a full suite of cGMP qualified analytical equipment to perform all the testing prescribed.
- Early adoption testing: Early adoption of the new chapters ensures packaging systems are compliant with the USP guidelines. It also enables drug developers to establish a robust testing history, or source and qualify alternative options should their current packaging systems fail to meet the requirements prescribed in the new chapters. Biotech or pharmaceutical companies that are early adopters will benefit by staying ahead of the requirements. For instance, they will be able to conduct risk-based decision making predicated on the comprehensive testing conducted and subsequent assessments.
Our Laboratory services team has practical experience testing a variety of packaging systems and plastic materials, and performing the plastic packaging, glass containers and elastomeric components requirements as described in the chapters of the three prime regional pharmacopoeia organizations (USP, European Pharmacopoeia and Japanese Pharmacopoeia).
Recently, a major U.S. pharmaceutical company enlisted PPD Laboratory services to establish USP-NF <661.2> compatibility with many of its existing oral-dosage form packaging systems such as blister packs, droppers and bottles. Our experts partnered closely with the pharmaceutical company to design and execute protocols that follow the compendial guidance and are tailored to the intricacies of each individual type of packaging system.
This collaboration proactively ensured the company’s packaging met all compendial requirements before the new guidelines go into effect.
Choose a partner that stays ahead of the curve with regulatory requirements and laboratory expertise
To proactively meet new USP guidelines, organizations must partner with a forward-thinking laboratory provider like the PPD clinical research business of Thermo Fisher Scientific. Our Laboratory services staff:
- Stays up to date with evolving guidelines and USP requirements
- Offers efficient testing turnaround times, including expedited testing options
- Has an experienced raw material testing team with dedicated technical and project managers
- Actively participates in industry groups and conferences to learn the latest in pharma packaging news, and are regular contributors to the top industry publications
Customers that partner with us achieve successful and early adoption of regulatory guidance — and maintain compliance and patient safety into the future.